Do 3D printed parts weld as well as forged parts?
-
Apr, 4 2023
-
0 Comments
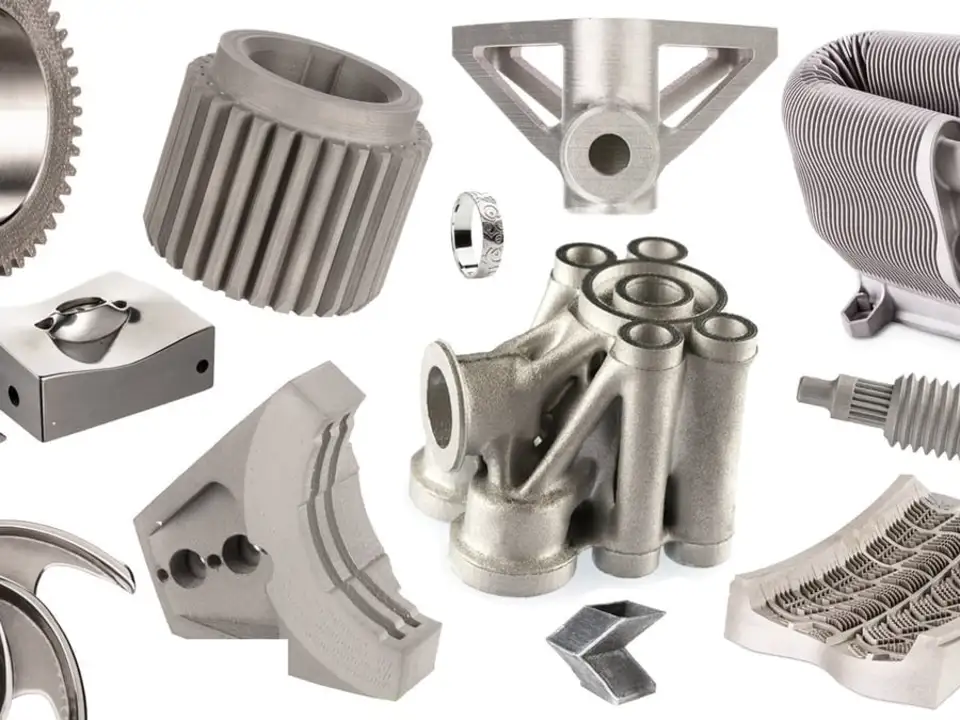
A Comparison of 3D Printed Parts and Forged Parts: What You Need to Know About Welding
When it comes to welding, the type of material used will have a significant impact on the success of the weld. There are various methods of manufacturing parts and components, including 3D printing and forging. Both of these processes have some advantages and disadvantages when it comes to welding. Here, we take a look at the pros and cons of 3D printed parts and forged parts and how they affect welding.
3D Printed Parts
When it comes to 3D printing, the technology has come a long way in recent years. 3D printing is a relatively inexpensive process that can produce complex parts with a high degree of accuracy and repeatability. This makes it ideal for producing parts that require intricate designs. 3D printed parts can be welded, but the process is more challenging than with forged parts. This is because 3D printed parts are more porous and have more irregularities on the surface. This can make it difficult to achieve a good weld. Additionally, 3D printed parts often require specialized welding techniques and materials that can be costly.
Forged Parts
Forged parts are manufactured by heating and shaping metal. This process produces parts with a much smoother finish than 3D printed parts. This makes it easier to achieve a good weld on forged parts. Additionally, forged parts can be welded with traditional welding equipment and materials, making it a less expensive process. However, forged parts require specialized tools and expertise to produce. This can make it more costly and time-consuming than 3D printing.
Conclusion
When it comes to welding, both 3D printed parts and forged parts can be used, but each has its advantages and disadvantages. 3D printed parts are less expensive and can produce complex designs, but the process of welding them is more challenging. Forged parts are easier to weld but require specialized tools and expertise to produce. Ultimately, the choice between 3D printed parts and forged parts for welding will depend on the design of the part, the complexity of the weld, and the budget available.
Exploring the Advantages and Disadvantages of Using 3D Printed Parts in Welding
3D printing is a revolutionary technology that has been increasingly used in many industries, including the welding sector. 3D printing is the process of creating three-dimensional objects from a digital file. This technology has been used to create parts for machines, prototypes, and other components used in welding. But the question on everyone’s mind is: do 3D printed parts weld as well as forged parts?
Advantages of 3D Printed Parts
3D printing offers several advantages for welding operations. One of the most important is that it allows for the rapid prototyping of parts, which can reduce lead times and cost. Additionally, 3D printing can be used to produce parts with complex shapes and intricate details that would be difficult to achieve with traditional forging methods. This can be beneficial for the production of parts for special jobs, such as those requiring customized parts. Finally, 3D printed parts are typically lighter than traditionally forged parts, which can reduce the overall weight of the machine or structure being constructed.
The Disadvantages of 3D Printing
Although 3D printing offers several advantages, there are some drawbacks to consider. For starters, 3D printed parts may not be as strong or durable as traditionally forged parts. This could be a problem in welding operations that require high levels of strength, such as those dealing with heavy machinery. Additionally, 3D printed parts may require additional finishing or coating, which can add to the overall cost. Finally, 3D printed parts may require specialized materials, which can be difficult to source or expensive to buy.
Weld Strength of 3D Printed Parts
When it comes to welding 3D printed parts, the strength of the weld is a major concern. Generally speaking, 3D printed parts weld just as well as traditionally forged parts. However, it is important to consider the material being used. The weld strength of 3D printed parts can vary depending on the material used, and it is important to ensure that the material is compatible with the welding process being used. Additionally, 3D printed parts may require additional steps to ensure a strong weld, such as pre-heating the parts or using specialized welding techniques.
Conclusion
In conclusion, 3D printing can be a great option for producing parts for welding operations. In most cases, 3D printed parts will weld as well as traditionally forged parts. However, it is important to consider the material being used and to ensure that it is compatible with the welding process being used. Additionally, 3D printed parts may require additional steps to ensure a strong weld. By considering these factors, it is possible to use 3D printing to produce parts for welding operations with confidence.
Examining the Strength and Durability of 3D Printed Parts When Used in Welding
3D printing has become a revolutionary way of manufacturing parts, but how does it fare when welded? To understand this, we need to examine how 3D printed parts and forged parts compare in terms of strength and durability when used for welding.
The main difference between 3D printed parts and forged parts lies in their manufacturing process. 3D printed parts are created using a layer-by-layer approach, while forged parts are subjected to extreme heat and pressure. This means that 3D printed parts may not be as strong as forged parts, but they can still be used in welding applications.
When it comes to strength and durability, 3D printed parts are less likely to break or crack under high temperatures than forged parts. This is due to the fact that the printing process creates a more uniform and dense material. This makes 3D printed parts more ideal for welding applications that require extreme temperatures.
However, 3D printed parts are more prone to warping, which can be an issue when welding. Warping is caused when the material shrinks or expands due to heat, making it difficult to maintain a precise fit. To prevent warping, it is important to use a higher temperature for welding 3D printed parts and to keep the temperature constant during welding.
When it comes to durability, 3D printed parts may not be as strong as forged parts, but they still offer good wear resistance and can withstand most welding applications. 3D printed parts are also more resistant to corrosion, making them a good choice for welding in moist or corrosive environments.
To conclude, 3D printed parts may not weld as well as forged parts, but they can still be used in welding applications. 3D printed parts are less likely to break or crack under high temperatures and are more resistant to warping and corrosion. However, they may not be as strong or durable as forged parts, so it is important to consider the application before choosing the right material for welding.
How 3D Printing is Changing the Welding Process: What You Need to Know
When it comes to welding metal parts, there have traditionally been two main methods for doing so: forged parts and 3D printed parts. But in recent years, 3D printing has become a viable option for quickly and efficiently creating complex parts. In this article, we'll explore how 3D printing is revolutionizing the welding process and what you need to know in order to take advantage of this technology.
3D printing offers a number of advantages over traditional forging methods. For starters, 3D printing is much faster and more cost-effective than forging. This means that parts can be printed quickly and with minimal waste. Additionally, 3D printing eliminates the need for expensive tooling and specialized machinery, resulting in lower costs and higher-quality parts.
In terms of welding, 3D printed parts offer a number of advantages. For starters, 3D printed parts are much more accurate than traditional forged parts. This means that welders can achieve a higher level of precision when welding 3D printed parts. Additionally, 3D printed parts are much stronger than forged parts, meaning that welders can achieve stronger welds with 3D printed parts than with forged parts.
But it's not just the accuracy and strength of 3D printed parts that makes them ideal for welding. 3D printed parts can also be customized to fit the exact specifications of a given project. This makes it easier for welders to get the exact part they need for their project, eliminating the need for costly trial and error when sourcing parts.
So, do 3D printed parts weld as well as forged parts? The answer is a resounding yes. In fact, 3D printed parts are often superior to forged parts when it comes to welding. This is due to the accuracy and strength of 3D printed parts, as well as the ability to customize parts to meet the exact needs of a project.
3D printing has revolutionized the welding process, making it easier and faster to create precision parts. By leveraging the power of 3D printing, welders can create stronger and more accurate parts than ever before. So if you're looking for a reliable and cost-effective way to create parts for your next welding project, 3D printing is the way to go.